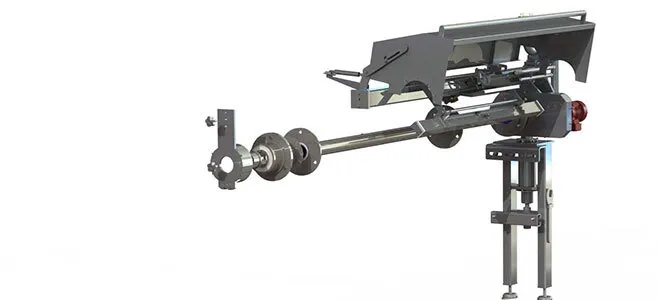
Berndrop® Pelletisers
The Berndrop® Pelletiser is a specialised type of industrial process machinery used for converting molten or semi-molten substances into uniform, solid pellets. It is particularly effective in handling materials that can be liquefied and require solidification into small, manageable pellets for ease of handling, transport, and further processing. The machine is widely used in the chemical, food, pharmaceutical, and plastics industries, where precision and consistency in pellet size are critical.
Key Features and Components:
1. Heating and Melting Unit: The raw material is first heated to a molten or semi-molten state. This unit ensures the material reaches the correct viscosity for optimal pellet formation.
2. Feed System: The molten material is fed into the pelletising system, typically using a pump or gravity feed. The feed system controls the flow rate, ensuring a consistent supply to the rollers.
3. Rollers: The heart of the Berndrop® Pelletiser is its set of precision-engineered rollers. These rollers are heated and work in tandem to form droplets of molten material. The rollers' surface can be designed with specific patterns or textures to influence the final pellet shape and size.
4. Cooling Belt: As the molten droplets are formed, they are deposited onto a stainless steel cooling belt or conveyor. This belt moves the droplets away from the rollers, allowing them to solidify into pellets as they cool down. The cooling rate can be controlled to achieve the desired pellet hardness and consistency.
5. Collection System: The solidified pellets are collected at the end of the cooling belt. Depending on the application, they may be transferred to a storage container, further processing, or packaging systems.
6. Control Panel: The Berndrop® Pelletiser is equipped with a modern control panel, allowing operators to adjust parameters such as roller speed, temperature, feed rate, and cooling time. This flexibility ensures that the machine can be fine-tuned for different materials and pellet specifications.
Applications:
• Chemicals and Polymers: Used for the production of uniform pellets from polymers, resins, waxes, and other chemicals, making them easier to handle and process in subsequent manufacturing stages.
• Food Industry: Applied in the production of food pellets, such as instant coffee granules, candy drops, or other confectionery products that require consistent size and shape.
• Pharmaceuticals: Ideal for creating pellets of active pharmaceutical ingredients (APIs) or excipients, ensuring precise dosing and uniformity in medication production.
• Specialty Materials: Suitable for the pelletisation of specialty materials like adhesives, sealants, or encapsulated substances, where precise pellet formation is necessary.
Advantages:
• Uniform Pellet Size: The Berndrop® Pelletiser ensures high consistency in pellet size and shape, which is essential for quality control in various industries.
• Efficient Solidification: The cooling belt provides an efficient and controlled environment for solidifying the pellets, ensuring they meet the desired physical properties.
• Versatility: Capable of handling a wide range of materials, from low to high viscosities, and producing pellets in various sizes by adjusting the roller design and operating parameters.
• User-Friendly Operation: The control panel offers easy adjustments and monitoring, reducing the risk of operational errors and enhancing safety.
Overall, the Berndrop® pastillator is highly efficient and versatile conveyor belt machinery designed to meet the stringent demands of modern production processes. It offers reliable performance, precise control over pellet characteristics, and the ability to handle a wide range of materials, making it an indispensable tool in various industries.
Pastillating Heads
Working alongside Berndorf band engineering means we are able to bring to market the latest generation of the pastillator head. With ongoing research and development ensures that this market leading technology will stand the test of time, with the support of trained specialists we can service and maintain this vital piece of equipment. Contact us for more information.